

From 1967 to 1971, he worked with special purpose finite element programs at the Westinghouse Electric Corporation. John is a Mechanical Engineer with almost 50 years of experience using the finite element method for engineering analysis. She earned her SB, SM, and PhD in Mechanical Engineering from the Massachusetts Institute of Technology. Kate is currently engaged in material and process research and development at GE Additive.

She has taught ANSYS and finite element analysis at the Massachusetts Institute of Technology (MIT) and has held faculty positions at the Korea Advanced Institute of Science and Technology (KAIST) and the Technical University of Denmark (DTU). Kate specializes in finite element modeling of microscale surface phenomena, parametric design, new product development, design for manufacturing, engineering design theory and methodology, and engineering design education and assessment. Kate is a Mechanical Engineer with almost 20 years of experience using ANSYS for engineering design and analysis in academia and industry. This provides a solid foundation on which to build, preparing readers to become power users who can take advantage of everything the program has to offer.

Exercises gradually increase in difficulty and complexity, helping readers quickly gain confidence to independently use the program. The book is written in a lecture/lab style, and each topic is supported by examples, exercises and suggestions for additional readings in the program documentation. Additional topics covered include an introduction to commands, input files, batch processing, and other advanced features in ANSYS. Students will find a practical and integrated approach that combines finite element theory with best practices for developing, verifying, validating and interpreting the results of finite element models, while engineering professionals will appreciate the deep insight presented on the program's structure and behavior. Click here to purchase from Rakuten Kobo ANSYS Mechanical APDL for Finite Element Analysis provides a hands-on introduction to engineering analysis using one of the most powerful commercial general purposes finite element programs on the market.
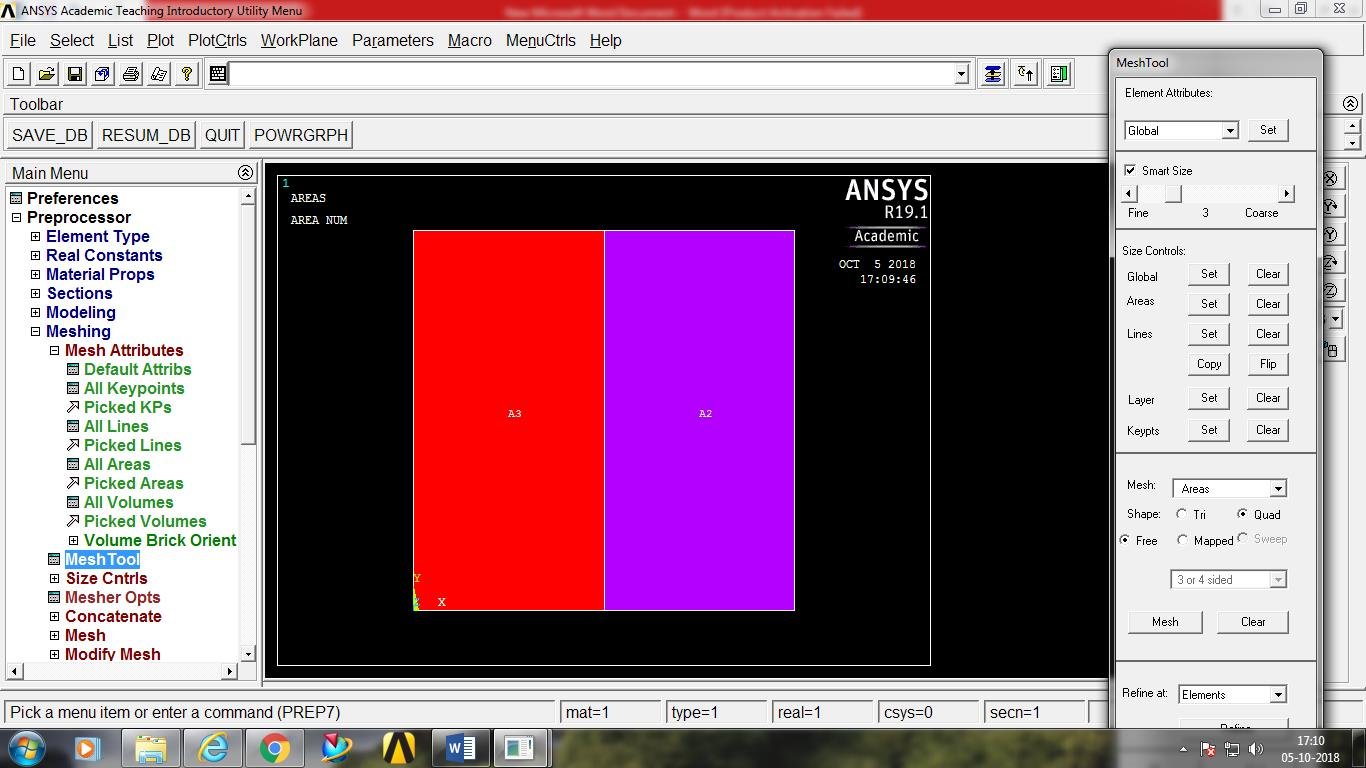
The adoption of an innovative and lightweight plastic housing for its steering system supports both the ecological and economical goals of thyssenkrupp Presta and helps the company lead the evolution of the steering systems for the automotive market of tomorrow.Also available on eBook for £62.09. Ansys Mechanical’s short fiber reinforced composite workflow helped thyssenkrupp Presta reach the targeted 50% weight reduction with respect to the original metal part to meet mechanical performance and OEMs requirements. Thyssenkrupp Presta is leveraging its longstanding competencies in materials, components and systems to lead automotive digital transformation processes. For the high-volume production models (body panels, frames, housings), an increasingly adopted technique is the manufacturing of critical components through injection molding with short-fiber reinforced plastics. Composite materials are key to making vehicles lighter so they can use smaller engines that consume less energy and produce fewer emissions. To do so, leading vehicle manufactures and their partners are embracing lightweighting and electrification. In the automotive industry, there is a global push to reach zero vehicle emissions by 2050 to satisfy consumer demand and increasingly stricter environmental laws. All products have an environmental impact, a fact customers are increasingly aware of as they take an interest in their carbon footprints.
